Slowing Down Fashion with the Natural Palette of India
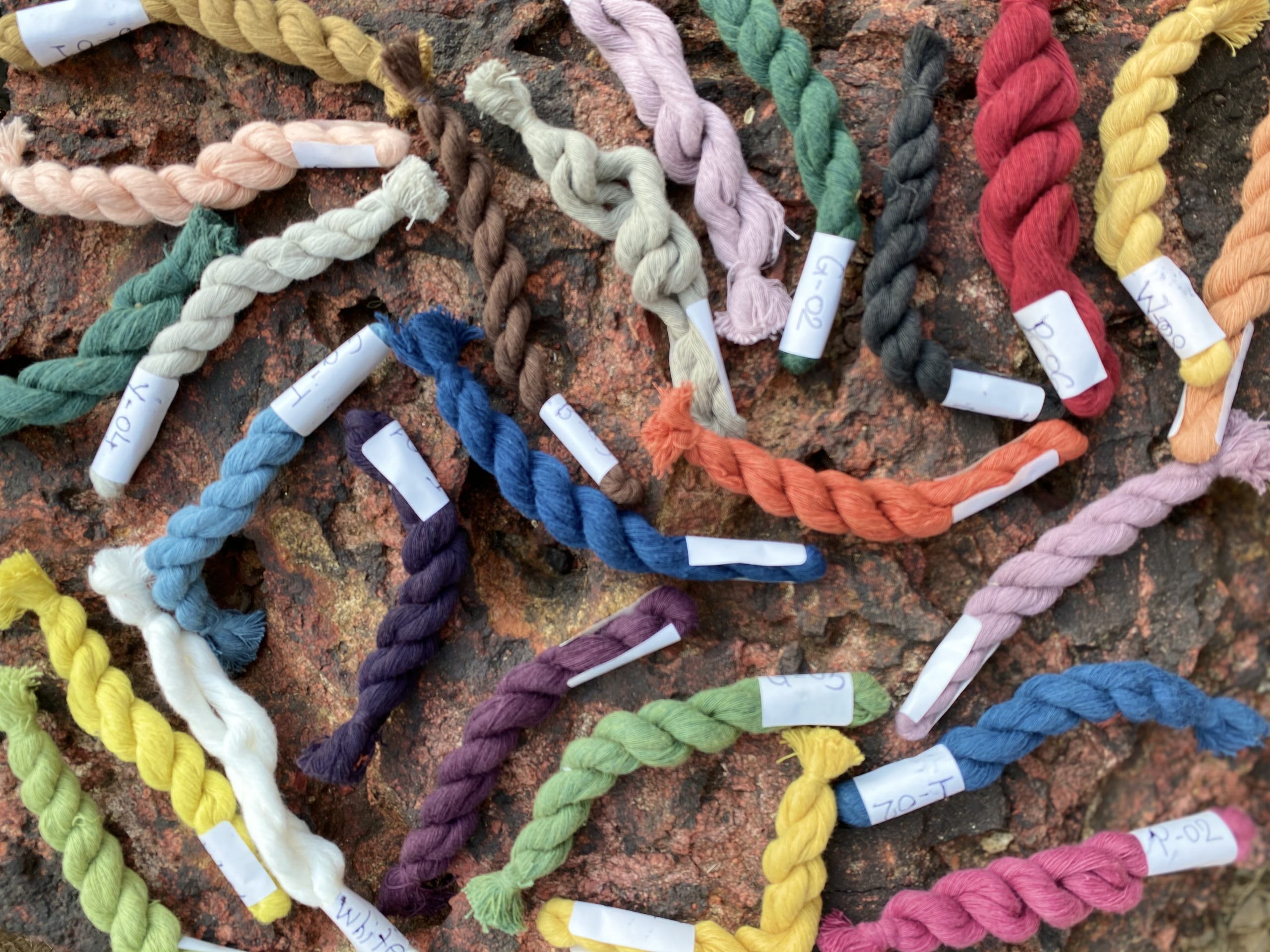
Dr. Bosco Henriques, the Founder-Director of BioDye India, which creates natural dyes for global labels such as Rachel MacHenry and homegrown labels including Ruchika Sachdeva’s Bodice, speaks about the natural palette of India, why isn’t it easy to scale up the natural dyeing process, and how to care for your sustainably dyed clothes
“My interest in natural dyes developed at the persuasion of my colleague Ann Shankar, who was working with widows in Punjab. She was a student of textile history. Ann knew that Indian textiles were at the heart of the spice trade, and were prized as heirlooms in East.
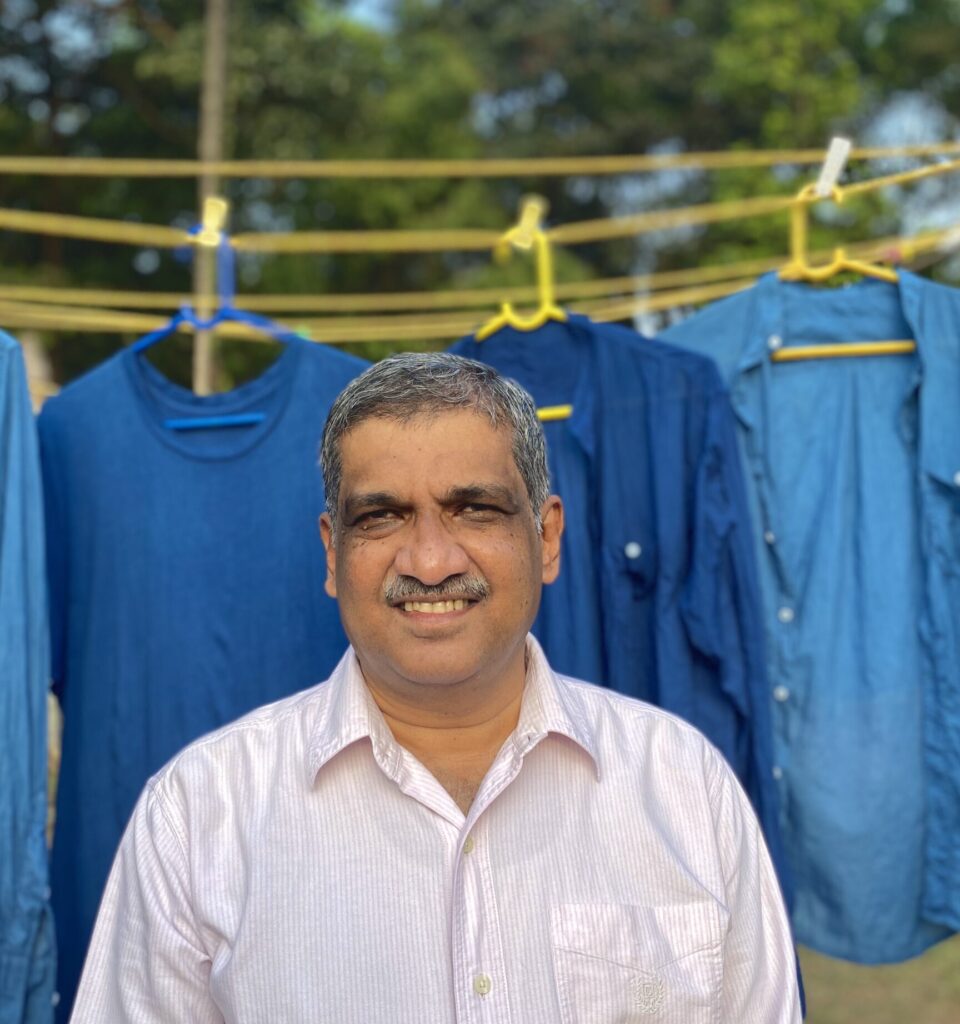
The widows knew how to weave dhurries, as they each had made one for their trousseaus. In the past, they would use their cooking vessels to extract natural dyes and colour the yarn. Now, they replicate the process with toxic synthetic dyes and empty the spent dye in their courtyards.
There is a marked difference between natural dyed and synthetic dyed yarn.
The colours in old durries made from the former were harmonious, whereas the same designs made with synthetic dyes were garish. This prompted Shankar to upgrade and revive natural dyeing techniques using modern scientific understanding. As I am a trained microbiologist and plant molecular biologist, she approached me to solve the problems associated with the fastness and shades of natural dyes. This was my initiation into the colourful world of natural dyeing.
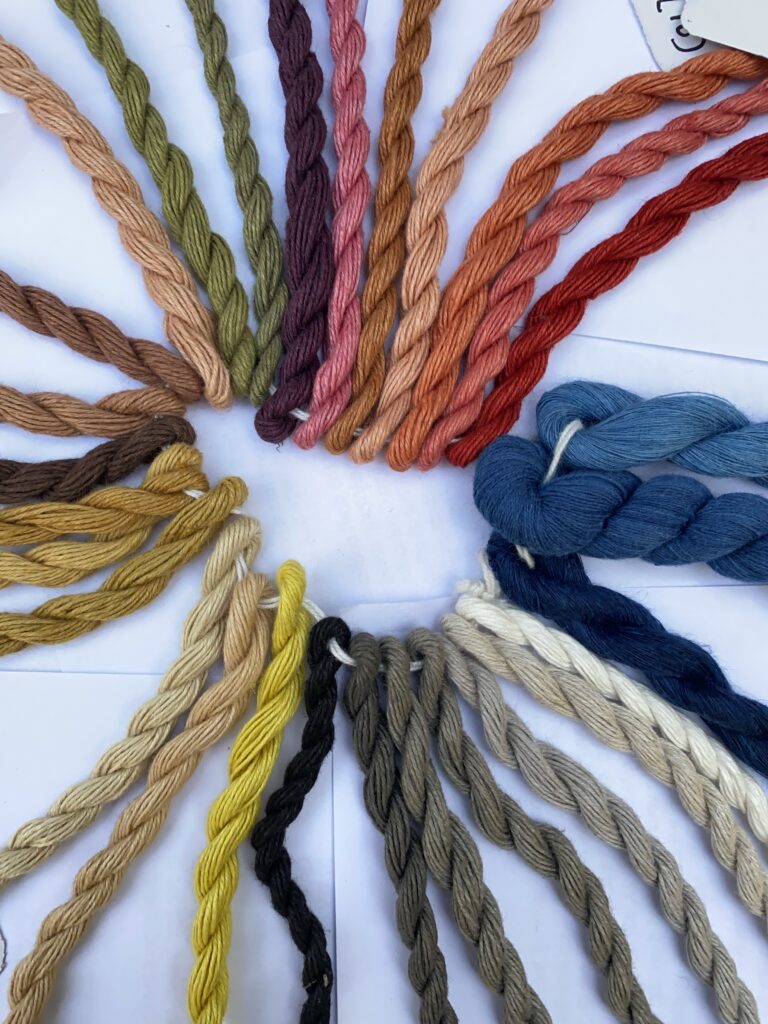
The problem with dyeing: the runoff
A technician working for an international company that set up effluent treatment plants for various industries worldwide informed me that only very large, integrated textile companies in India could set up such plants that could treat textile effluent in an economic manner as per prescribed standards. The capital cost was prohibitively expensive, as steel or titanium was needed to fabricate some of the equipment. Operating that was costly due to an excessive consumption of energy. The burial of the resultant solid hazardous waste was also a problem.
Currently, I am unaware of how many Indian dye-houses are able to meet the prescribed standards and still be economically competitive in the domestic and export market. Having said that, newer dyes and dyeing machines have lowered the concentration of spent dye and auxiliaries in the waste-stream. They have also lowered the quantum of effluent discharged.
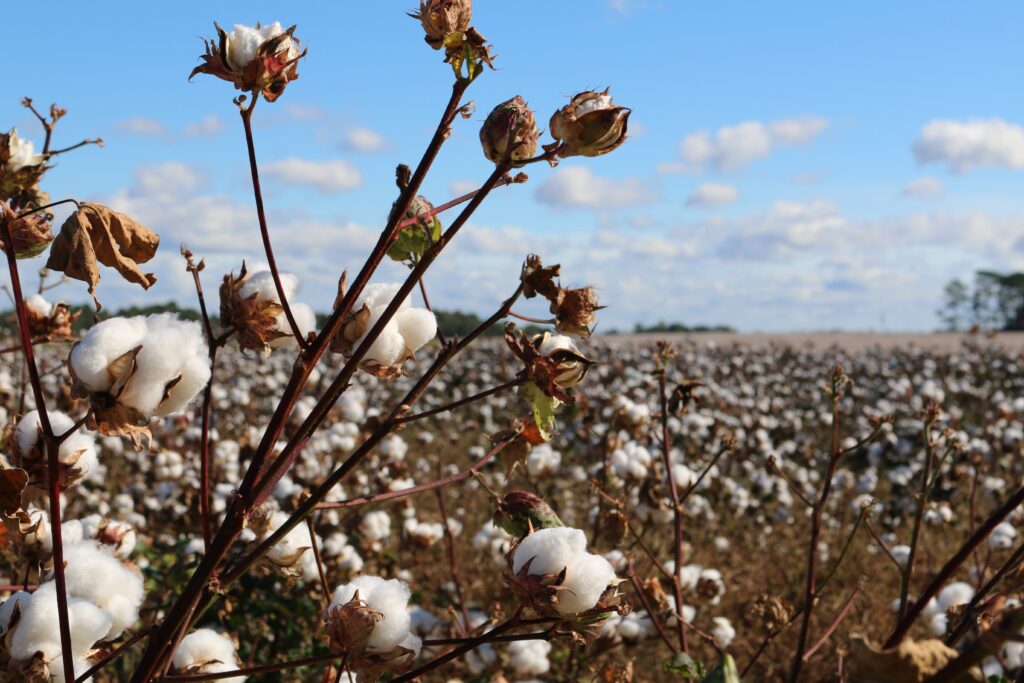
Synthetic v/s natural dyes
The obvious: synthetic dyes are cheap, while natural dyes are expensive. Natural dyes are presently scarce and need to be stocked, whereas synthetic dyes are available on demand. Indigo is the only blue natural dye available and it is ozone sensitive (so is synthetic indigo). Non-indigoid blues are available in the case of synthetic dyes. Synthetic yarns and fabrics (except nylon) cannot be dyed with natural dyes. The fastness of colour of BioDyed fabrics and yarns and synthetic dyed fabrics and yarns are similar.
Natural dyes used by us are hypoallergenic, while many synthetic dyes cause allergic reactions. The treatment of natural dye’s effluents is simple and the treated waste-water can be used for irrigation. Synthetic dye effluents need expensive treatment plants to create reusable water.
Solid waste from natural dyeing can be composted and used as manure, but the solid waste from synthetic dyeing is hazardous and needs to be buried in lined pits.
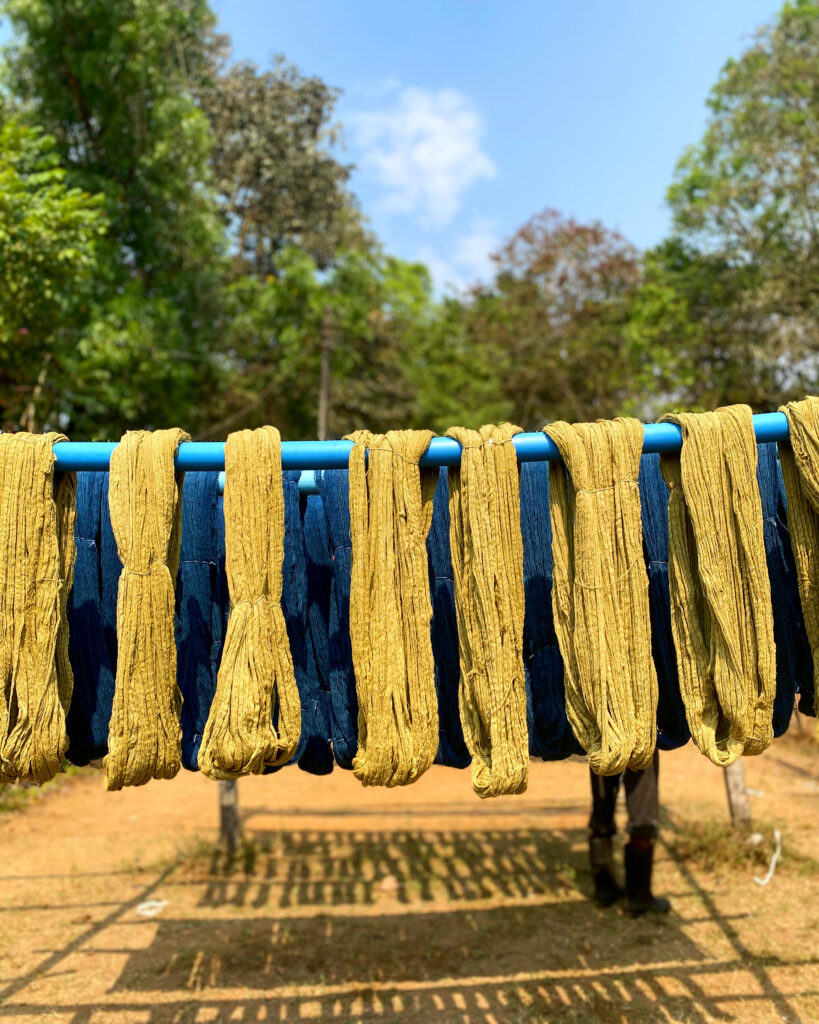
The Pantone shade card
We primarily dye for foreign buyers. They often give us a Pantone shade that has to be obtained by a combination of three dyestuffs. This is difficult to achieve. Especially when it has to be reproduced over the years with different raw material batches.
So far, we have been able to reproduce the Pantone shades our clients have selected.
We mainly use plant-based colourants: indigo (fermentation vat) for blue, leaves for yellow and earth hues, cutch (by-product of catechu manufacture) for brown, vines of Indian madder and lac (insect dye) for red, and iron vinegar for black and grey.
Alum and iron are the only mordants used (chromium, tin and copper are not used). Wood, roots and bark are not used as their harvesting would kill the plant.
A few things need to be kept in mind. Shades which contain a low concentration of dye substance are difficult to dye evenly. Exact neutral colours (creams, greys), that are neither warm nor cold, are also difficult to reproduce. Double dyeing, namely, indigo +yellow or red to yield green or purple are hard also to achieve.
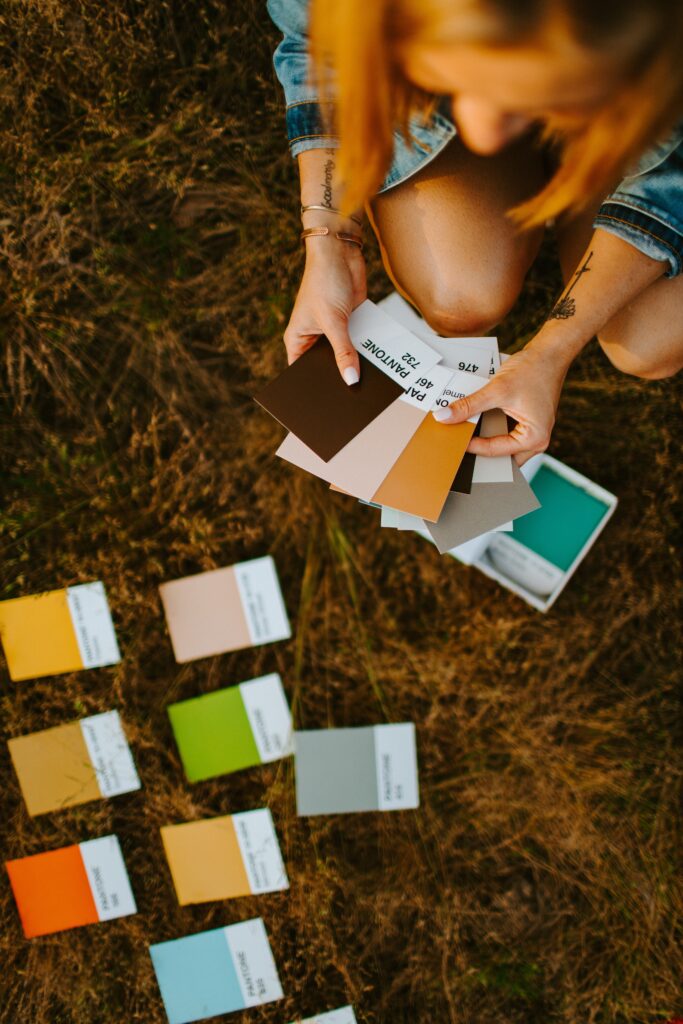
Challenges in natural dyeing
When I entered the field, naturally dyed fabric had a reputation of fading in sunlight. It also had a reputation of bleeding during washing and smudging with perspiration. Few hues and tones could be obtained, and they too were pallid and dull. Dyeing was a cumbersome, long process.
The processes subsequently developed by me shortened the dyeing time, gave the entire spectrum of colours that were bright, vivid and bound fast, resistant to light, wash, crock and perspiration. This was done using only non-toxic and biodegradable inputs. Caustic lye was not used to scour greige cotton yarn or fabric. Enzymes prepared in-house were used instead. This allowed us to use our waste water for irrigation as it was not salty. We are now installing dust collectors on our stoves to limit air pollution. Eventually, we plan to use solar energy to heat our water and provide most of our electricity.
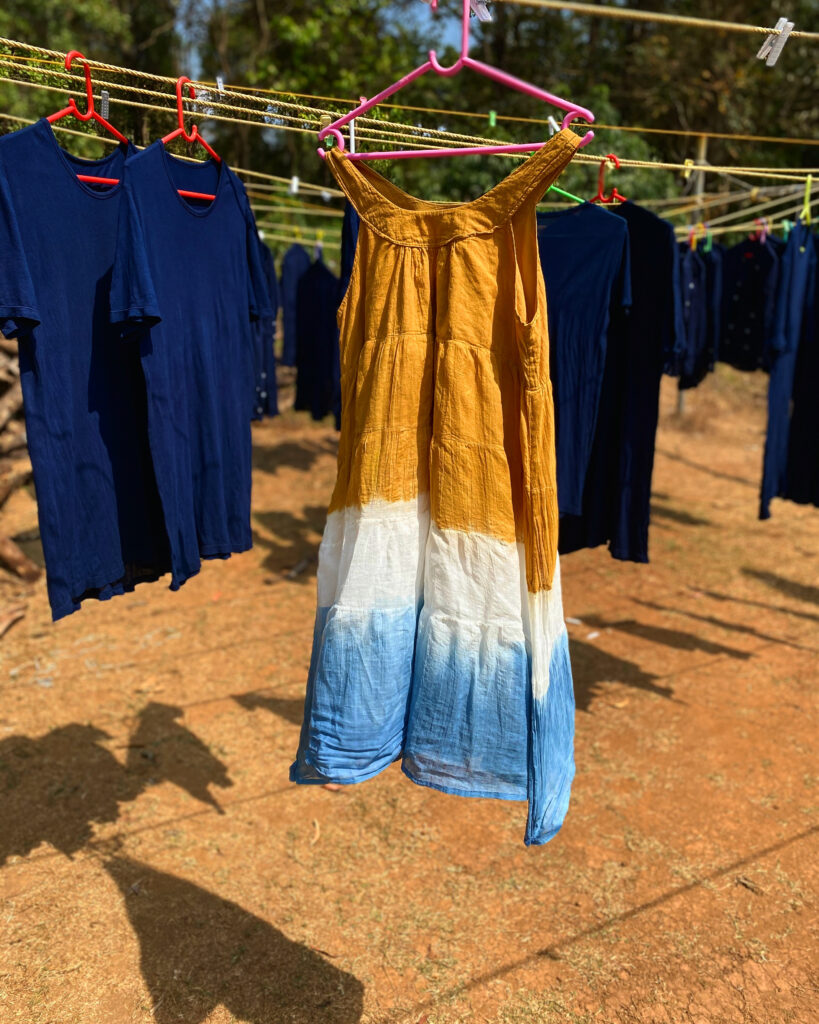
Caring for naturally dyed clothes
Many wonder what is the correct way to maintain naturally dyed apparels. Instructions for fabric-care are to wash natural dyed yarns and fabrics in soft water, using pH neutral anionic detergent, devoid of chelators (small molecules that bind very tightly to metal ions). Do not use bleach and do dry yarns and fabrics in the shade.
Keep shaded garments dyed in indigo away from ozone. Exposure to acids, alkalis, carbonic acid salts, bleaching agents, heavy metal compounds, chelators and stains will alter the shade. Some colours can get tanned when exposed to strong sunlight. Black yarn should be stored under aerobic (exposed to oxygen) conditions. In India, Ezee and Genteel liquid detergents are recommended and Ecover Delicate liquid detergent can be used abroad.
The future of natural dyeing in slow fashion
Fast fashion needs to be cheap and hence depends on synthetic dyeing which is polluting.
Even properly treating the synthetic dye waste pollutes the air (as it is energy hungry) and land (landfills for the hazardous sludge). The cost of synthetic dyeing is not properly captured. The marginalised endure it and the whole society ends up paying for it, thereby subsidising it.
Eventually, we need to find agricultural models that scale up natural dyeing.
We are experimenting with indigo as an inter-crop and rotation crop. We have developed the agro-technology to cultivate Rubia sikkimensis (Indian madder from Sikkim, Arunachal Pradesh, Nagaland and Manipur). As authentic raw material is scarce, we can cater only to the high-end niche market. When the supply of raw material increases, and dyeing of all the shades can be mechanised, will the prices decline and natural dyeing can reach a wider market. But natural dyes can never cater to fast fashion that discards perfectly wearable clothes.
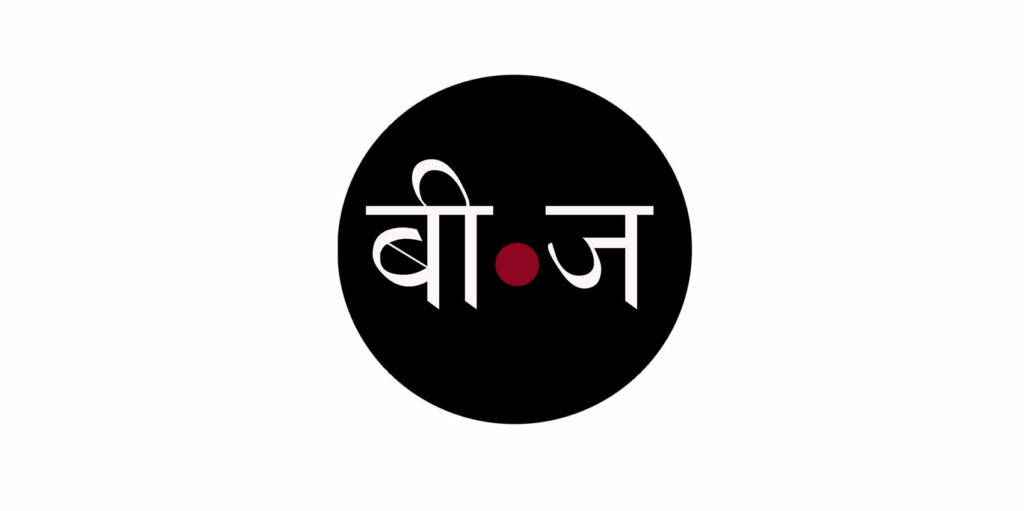
Most Read Articles
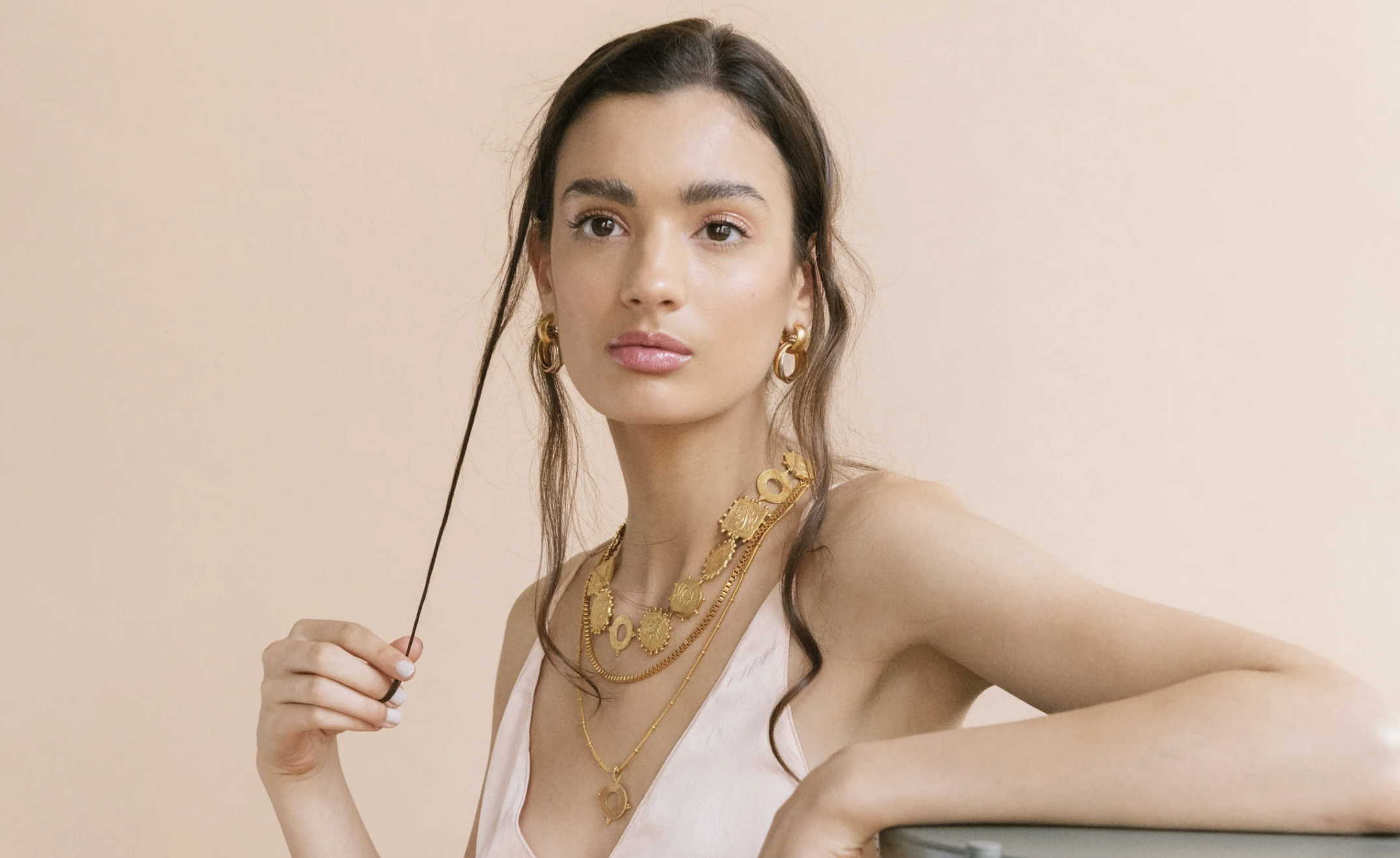
A Complete Guide to Demi-Couture Jewellery in India
The ultimate guide to artistic baubles and demi-couture jewellery that evokes the splendor of India... Read More»
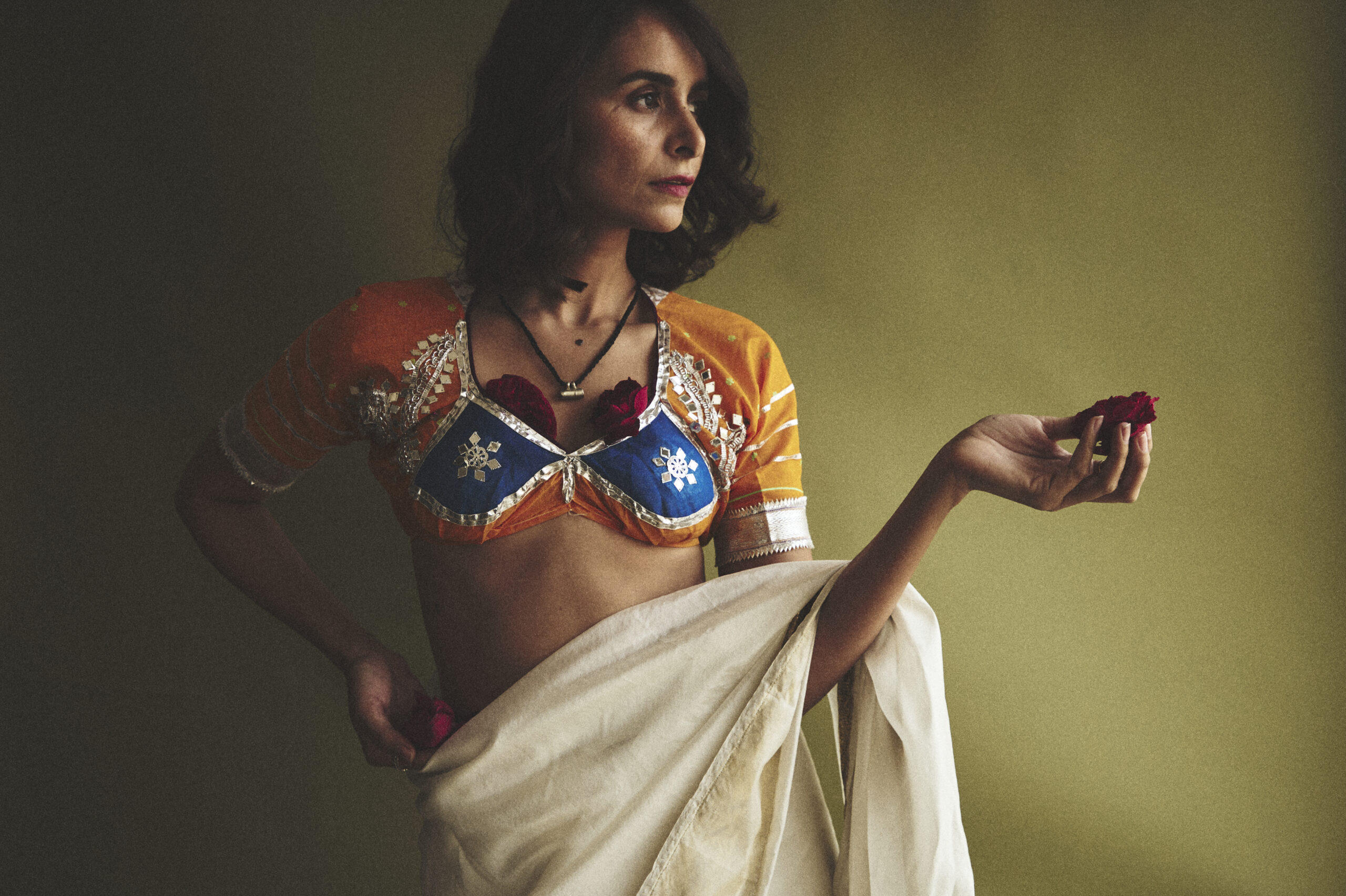
Rajasthan’s Aangi Finds New Life in Aangiwali’s Fusion of Tradition and Style
Aangi is a garment woven with history. In the arid landscape of Shekhawati, Rajasthan, it... Read More»
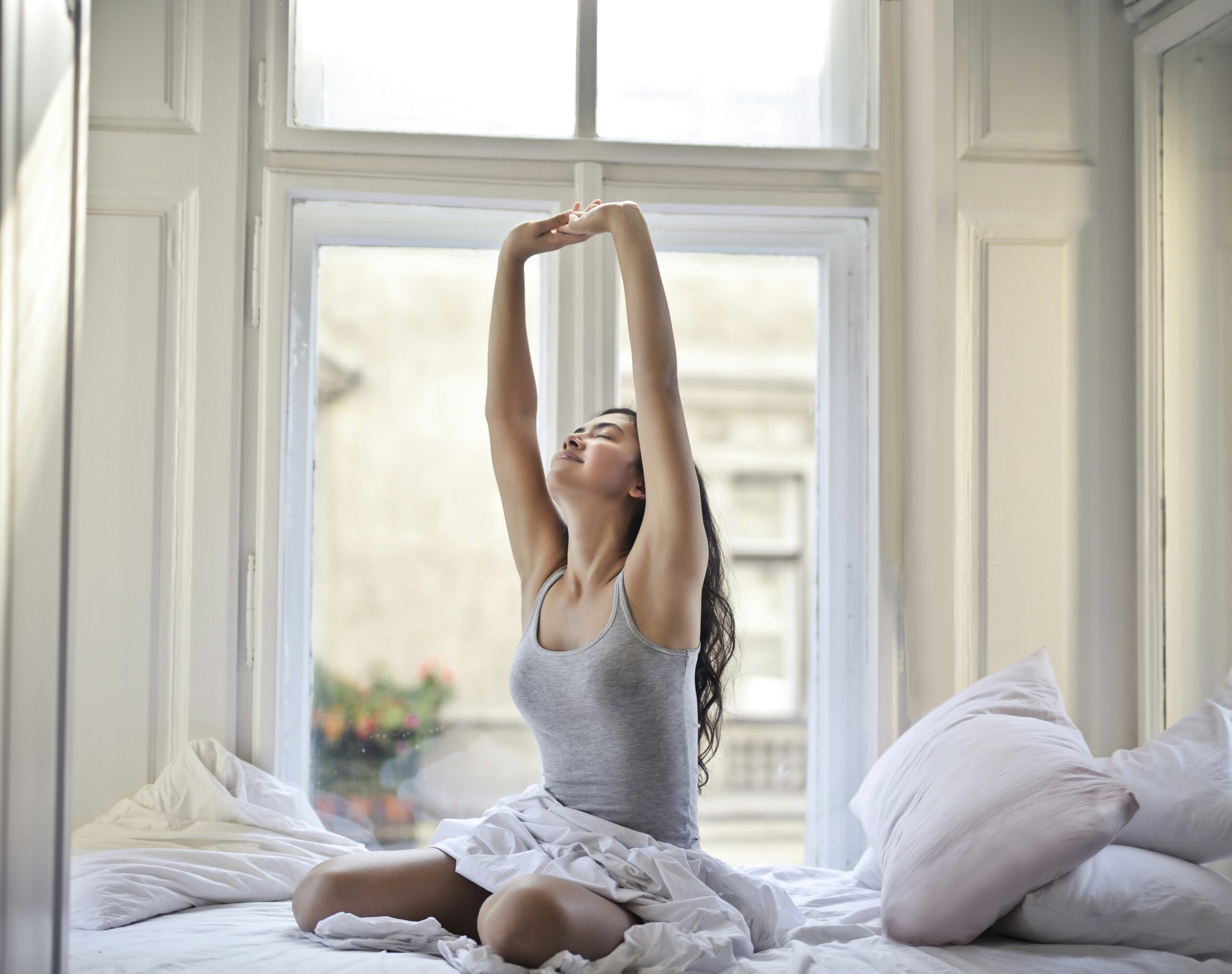
The Ultimate Guide to the Best Natural Deodorants in India
The top 12 natural deodorants that banish BO and nix nasties for round-the-clock freshness Our... Read More»
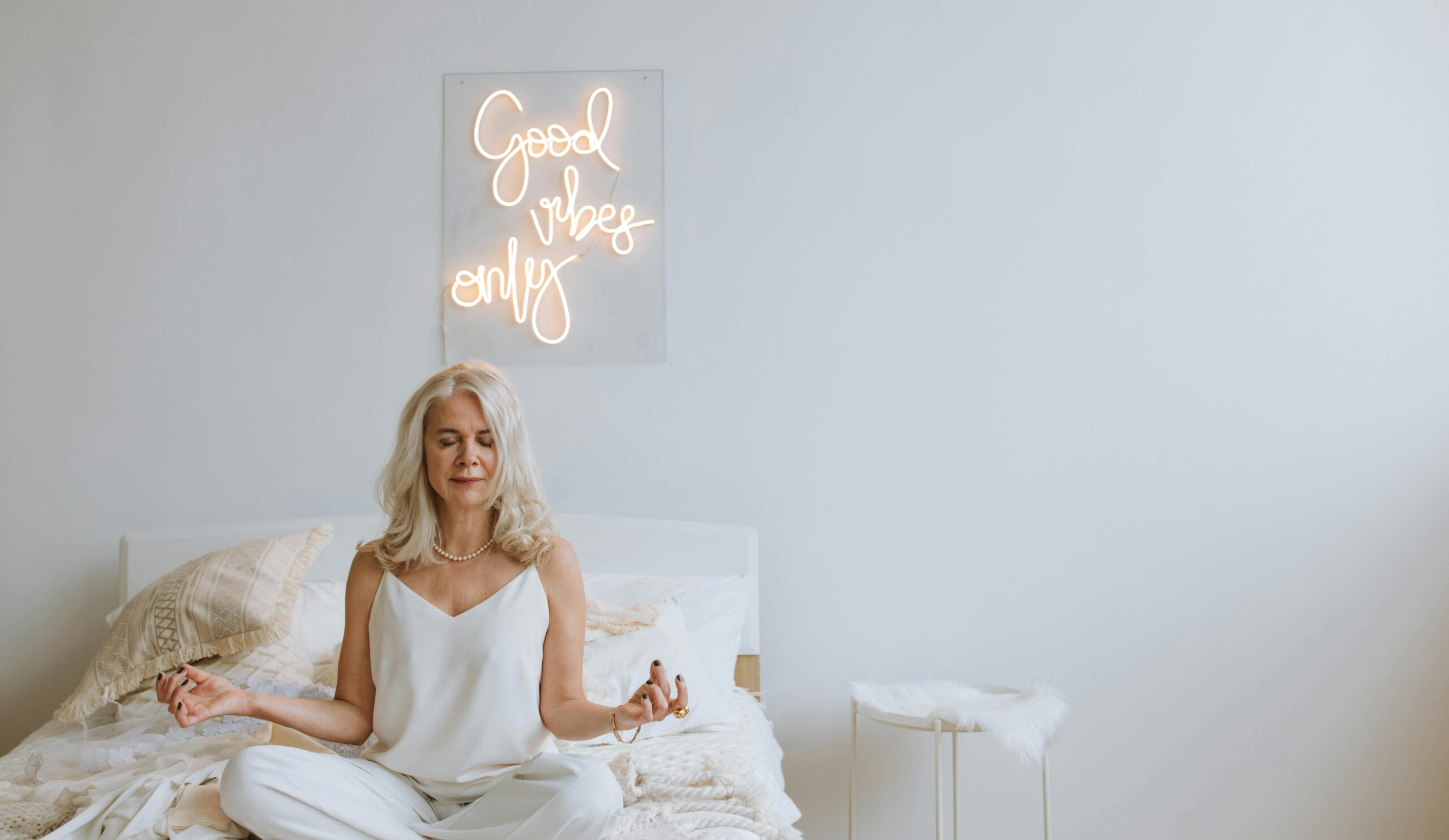
Easy Yoga Practices for Menopause Relief
Dr Hansaji Yogendra, Director of The Yoga Institute and President of the Indian Yoga Association... Read More»